Should we give up control charts when we find ourselves faced with “non-standard” situations that do not verify the hypotheses of use of the MSP? On the AFNOR standard side, no answerDaniel Lafaye de Micheaux here proposes a clarification of the definition of the limits to be used for process control. Going beyond the framework of the classic monovariate PSM, this definition introduces the notion of specific multivariate indicators of anomaly and that of the Alarm Index, pHow to go further in the Statistical Control of Processes? MSP indeed has its limits, in an industrial context where quality and productivity requirements are increasing, where industrial processes are becoming more complex, where the number of measurements to be processed and monitored is ever greater. GPC technology, “Global Process Control”, is an extension of MSP. It offers a radically innovative approach to processes, a “global” approach.
Should we give up control charts when we find ourselves faced with “non-standard” situations that do not verify the hypotheses of use of the MSP? On the AFNOR standard side, no response. Daniel Lafaye de Micheaux proposes here a clarification of the definition of the limits to be used for process control. Going beyond the framework of the classic monovariate MSP, this definition introduces the notion of specific multivariate indicators of anomaly and that of Alarm Index, specific to the GPC technology. Its application allows the development of relevant graphs to quickly identify the most critical malfunctions.
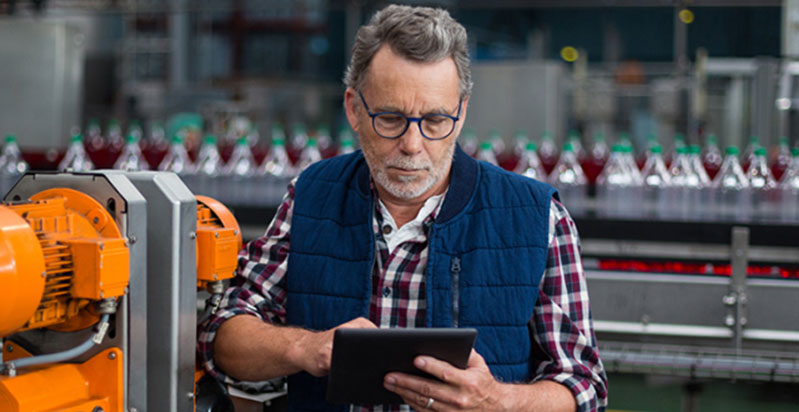
Qualité références : La MSP les situations non standard
Should we give up control charts when we find ourselves faced with “non-standard” situations that do not verify the hypotheses of use of the MSP? On the AFNOR standard side, no answer offered. Daniel Lafaye de Micheaux, R&D director of GPC System, and Alain Palsky, former MSP manager of the Rhône-Poulenc group, present here how to adapt the use of control cards to these “non-standard” situations.
Four posts are available here:
In this presentation, Mr. Daniel LAFAYE DE MICHEAUX presents a problem encountered. Traditional MSP is based on individual monitoring of parameters to be controlled; this so-called “one-dimensional” approach has the disadvantage of not taking into account the links between the parameters and therefore too often tends to implicitly assert “I see nothing = nothing happens”.
Daniel Lafaye de Micheaux and Didier Vieux rely on the industrial experience of GPC System to show how multivariate vision improves the profitability of production lines. If the serious phenomena affecting them (long stoppages, rejects, customer returns, etc.) are often invisible on the monovariate control charts, they are on the contrary clear and clearly identifiable in multivariate vision.
This article presents the use of “Global Process Control” technology to reduce variability in industrial production. This text applies to give the bases of the GPC methodology used for this purpose. It describes the implementation steps on an industrial example of automobile body assembly.
In this presentation, Mr. Daniel LAFAYE DE MICHEAUX presents a problem encountered in the field of plastics processing in relation to plastic injection presses before addressing: the GPC approach to curve analysis; the construction of indicators; GPC multivariate monitoring of indicators and real-time monitoring.
In this presentation, Mr. Daniel LAFAYE DE MICHEAUX presents a problem encountered in the automotive industry concerning production monitoring before highlighting the fundamental points of GPC System.
In this presentation, Mr. Daniel LAFAYE DE MICHEAUX, presents the fundamentals of the Global Process Control technology and the services offered by GPC System.